The dimensions for the model HUMVEE were found from direct
measurements taken from an actual HUMVEE as well as measurements
estimated using CAD software and photographs. Once all of
the necessary dimensions for the HUMVEE were found, CAD drawings
were created to ensure that the parts could be fabricated with
the available materials. Due to the large size of the
HUMVEE model, it was necessary to build the model in a way that
it could be disassembled in order to move it. It would be
necessary for the HUMVEE to be separated into pieces small
enough to fit through a standard doorway. Once the CAD
drawings were completed and met the required specifications, the
fabrication of the model HUMVEE was started. The body of
the HUMVEE was cut from sheets of plywood using a jig saw.
Two-by-fours were used for support and for connecting the
separate pieces of the plywood together. A miter saw was
used in order to quickly and accurately cut the two-by-four
lumber.
Once
all of the body pieces were cut from the lumber, they were
pieced together using various length wood screws. In order
to keep the system as hidden as possible, the air compressor was
stored undelumber. r
the hood of the HUMVEE. A firewall was placed between the
passenger compartment and the hood area in order to keep the air
compressor away from the passengers. The air hose was
connected to the air tank which ran to the side of the vehicle.
A switch was installed on this part of the air hose in order to
control the blasts of air. A hole was drilled into the
firewall so that the air hose could be passed into the passenger
compartment. This hose was then connected to an air
manifold which split the single line into five separate lines.
Each one of these lines would run to their respected air nozzle
as seen below.
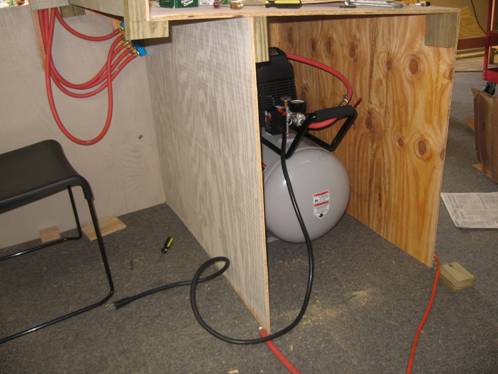
Each of the five hoses was run against the interior wall of the
HUMVEE as seen below.
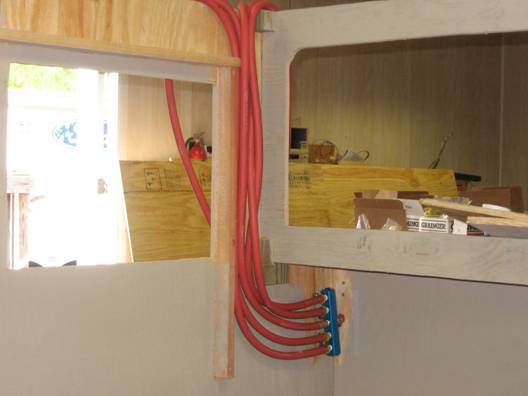
The entire length of hose was then enclosed within a small
wooden casing in order to hide the system. The nozzles
were connected to the air hose using the designated set of
fittings. Each nozzle was connected to a swivel type
fitting allowing some adjustability to different size passengers
within the vehicle. Holes were drilled in the wooden
covering allowing the nozzles to protrude at their desired
location.
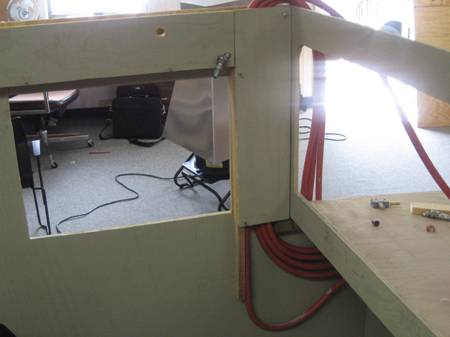
A
hole was drilled through the roof of the HUMVEE model to allow
the aerial nozzle to be placed. The aerial hose was run up
a two-by-four support and mounted to its proper location, shown
below.
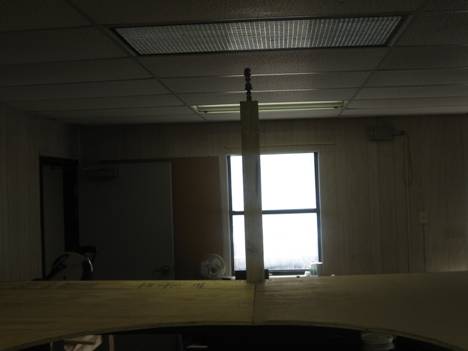
In order to reduce the risk of air leaks, all hose connections
were secured by hose clamps and all pipe connections were sealed
using pipe tape.
Interior and Exterior views of the completed model can be seen
below.
|