Fuel injection System
Spray Characterization
Spray
Characterization
In
order to verify that we have successfully
designed a spray system that achieves the desired droplet size we must
characterize the spray. Spray characterization will include
determination of
droplet size and distribution at various locations within the flow
field. The
method that we believe will be the cheapest and allow us to utilize
existing
equipment is a laser illumination system.
This system consists of a pulsed laser
illumination source, beam
diffuser (beam expander) and a high speed camera. This configuration
allows us
to capture a 2-D slice of a 3-D flow. This will permit us to quickly
determine
the ideal location for the placement of an ignition source based on
droplet
size. It should be noted that the flow velocity will have some effect
on the
flame front depending on the type of flame initiation and initial
energy input.
The
target values as stated by the Air Force
is a location within the spray where the mean droplet diameter can be
determined to be at the range desired for each test run. Using the flow
visualization techniques suggested previously the entire flow can be
quickly
evaluated to locate the desired conditions. In addition to the target
size
droplets being identified we can also identify areas of the spray where
ignition may more easily occur. Such areas where fine mist and large
droplets
coexist may be easier to ignite than areas weighted by a larger number
of large
droplets.
In
order to keep the characterization of the
nozzle repeatable variability in the test area must be eliminated.
Standard
test procedures for spray characterization should account for the
following
environmental factors. To minimize flow disruption we must ensure that
there
are no external sources of wind in the test area. The test area air
will be at
approximately room temperature and all testing should be done at a
relatively
constant temperature. The temperature of the fuel will greatly affect
the rate
of fuel droplet break-up by decreasing the vapor pressure of the fuel,
thus
allowing the fuel to atomize more freely. Therefore the fuel
temperature will
need to be kept constant. The testing will need to cover a number of
different
fuel delivery pressures to find the ideal operating conditions for each
nozzle.
Minimal
System
This
system is most effectively used with a
laser and diffuser screen to create a laser light sheet. Spreading of
the beam
can also be accomplished my directing the laser through an optical
quality
glass rod. Also it is necessary for this laser source to be pulsed in
order for
us to utilize a strobe-like effect to capture the still image. The
imaging
system which is available to us through the AFRL is capable of a FPS
(frames
per second) speed of 30000 which is much faster than necessary for our
purposes. If the frame rate can be reduced to 100 FPS then we can
significantly
increase picture quality and image resolution which will aid in manual
droplet
sizing.
Test System
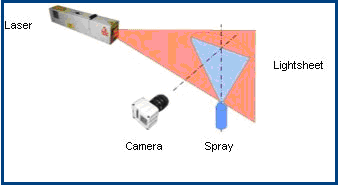
Figure: “Oxford
lasers: Imaging Division”
Typically
the system setup is simple. The
components include a laser light source in a visible spectrum of about
500
nanometers in wavelength. Commonly used is a green Nd:YAG laser between
200W
and 1000W peak output. A beam spreader/light sheet generator is used to
diffuse
the beam into a flat sheet. The optical system could be a high speed
film
camera, CCD camera, film camera, or a digital camera. In order to
minimize cost
we will attempt to utilize a high speed camera provided by our sponsor,
which
is capable of frame rates as high as 30,000 FPS. However, due to the
degradation of picture quality at 30k FPS we will operate at
approximately 30
FPS and if necessary we could increase the rate until we achieve the
appropriate image quality best suited for the flow characterization.
In
order to process the image to find the
target droplet size the images must be manually evaluated. This will
include
setting up the test area with reference grids. Then counting and sizing
the droplets
for each area of interest. This approach is recommended only when
testing
involves a few events and where the droplet size is large enough to be
visually
compared to a reference.
Suggested
System(s)
Alternatives
to manual count and measure
system include both imaging and non-imaging systems. Imaging systems
utilize
programs that count the number of droplets per image. Non-imaging
techniques
include Phase Doppler Interferometer (PDI), laser diffraction analyzers
and
optical probe arrays. In this phase of the design we would be best
suited to
use the imaging technique to quickly and cheaply confirm that we have
either
reached our target or not. This would allow us to develop procedures
for
producing suitable droplets consistently. However, to provide the means
to
baseline a CFD model, we would highly recommend a non imaging system. A
PDPA
system with the supporting software can gather the necessary data in
real-time.
This would greatly increase the number of validation tests that can be
performed. The PDPA system is a flux measurement device that measures
droplet
size and velocity as well as distribution within the “probe
volume”. The
following description from Spraying Systems Co. describes the general
PDPA
system.
"Phase
Doppler particle analyzers (PDPA)
PDPA are
flux sampling instruments and fall into the non-imaging (single particle
counter) category. These analyzers consist of a transmitter, receiver, signal
processor and computer. The PDPA uses a low-power laser that is split into two
beams or four beams for a 2-dimensional system. By utilizing a beam splitter
and frequency module; these laser beams intersect again at a point referred to
as the probe volume. When a drop passes through the probe volume, the scattered
light forms an interference fringe pattern. The scattered interference sweeps
past the receiver unit at the Doppler difference frequency, which is
proportional to the drop velocity. The spatial frequency of the fringe pattern
is inversely proportional to the drop diameter. A data analysis routine is used
to convert the raw drop count into a meaningful drop size distribution. The PDPA measures sizes in the 0.5 to 10,000
μm range using various optical configurations……." (Spray Systems Co.)
There are
several manufacturers of Phase Doppler analyzers:
• Artium
Technologies, Inc., Sunnyvale,
CA
(http://www.artium.com)
• Dantec
Dynamics A/S, Skovlunde, Denmark
(http://www.dantecdynamics.com)
• TSI
Incorporated, Shoreview, MN (http://www.tsi.com)
(Spray Analysis and Research
Services (manual), pg.
11)
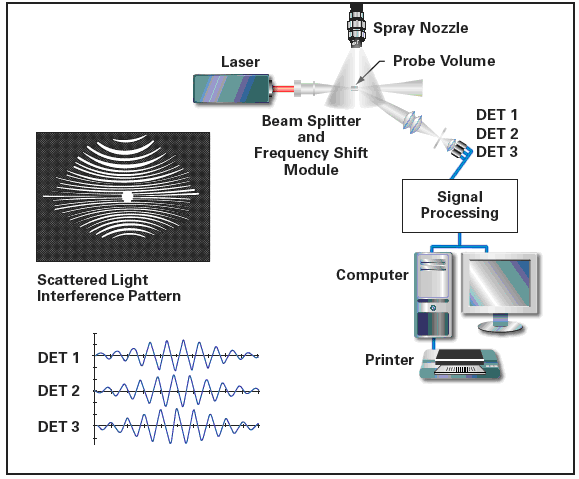
Phase Doppler Particle Analyzer:
Figure courtesy of
Spraying Systems Co.: “Understanding Drop Size”
In
order to effectively relate the flow
conditions to parameters readily usable by CFD modeling software a
complete
system offered by a laser imaging company should be used. These
companies
provide hardware and software that can rapidly evaluate the flow and
provide
data that can be more easily related to the CFD model, thus allowing
verification of the model.
Suggested
systems include the following:
“Artium
Technologies Inc.’s PDI–X00MD is a
modular system based on a laser Phase Doppler Interferometer. This
system
consists of an optical transmitter, receiver, signal processor and
software.
Most importantly the software which is called
“Aims” can provide droplet size
and velocity information. It is not indicated whether or not that this
system
provides correlations to volume flux and statistical analysis or is
these
values have to be calculated independently.
From
TSI Incorporated the PDPA-System
1-component (velocity measurement) system is appropriate for the flow
evaluation. It includes an emitter, receiver, signal processor and
analysis
& graphics software. This system provides data analysis on
droplet size,
velocity as well as statistical analysis with the provided
“Flowsizer 2.0”
software. This system also provides graphical representations of the
flow
characteristics and statistics in easily read charts.
Oxford
laser systems incorporated has a laser based system which falls into
the
optical analysis category. This system utilizes software to count and
measure
droplets related lens and focal length. This system may be suitable for
our
needs. However, one must consider whether or not the spray pattern
might
obscure the inner areas of the flow.
The
software in this system provides size, velocity and statistical data,
in easily
read graphs. It also provides a picture test area which is valuable in
determining non-spherical droplet characteristics.
Of
the three preceding systems the most
desirable is the TSI PDPA system. This company offers the most
accessories and
provides a significant amount of detail in their methods. Also, their
accompanying software provides more flow analysis than the other
companies.
Statistical
Analysis
Volume
Median Diameter (VMD) will be used to
represent the spray droplet size due to its wide spread use by
manufactures.
This will give the ability select and test nozzles that will deliver
the
desired droplet size. The VMD is based on relating the droplet size to
the
total fluid volume. Specifically the VMD is where 50% of the fluid
volume is
accounted for in droplets smaller than the target value, and 50% of the
fluid
volume is accounted for in droplets larger than the target value. Also
it may
become necessary to find regions within the flow that have different
characteristics. For certain tests areas with a large population of
small
droplets and few large droplets might be preferable. Locating these
areas can
be done by tabulating the droplet sizes (at varying pressures,
distance…) into
a histogram which would relate size to frequency of occurrence. In such
a case
the VMD would not be used, however it is an important tool in
standardizing
each test and a starting point in the classification of the nozzle
characteristics.
Reference:
NISTIR
6640: Thermochemical
and Thermophysical
Properties of JP-10
Bruno, Huber,
Laesecke, Lemmon, Perkins
National Institute
of Standards and Technology, June 2006
Combustion
Engineering
Borman, Ragland
McGraw Hill, 1998
Fluid
Dynamics
Moscow:
Maik, Nauka.
Handbook
of Mathematical Fluid Dynamics
Friedlander, Serre
Fluid
Power Dynamics
Mobley
Fluid
Dynamics and the Transport of Droplets and
Sprays
Sirignano
Fuels of Opportunity:
Characteristics and Uses in Combustion Systems
Tillman
Combustion
Chemistry: Elementary Reactions to Macroscopic
Processes
Faraday Division,
Royal Society of
Chemistry
Numerical
Study On the Formation of Spray Cloud By
Explosive Dispersal of Water Willed in V-shaped Trough
J.C. Liu, J. Ding,
Y.T. Hu and L.F. Xie
Website:
www.spray.com
An
Engineer’s Practical Guide To Drop Size
By
Rudolf J. Schick
Spraying
Systems Co.
1997
|